

Designed by noted architect Frank Gehry, the Peter B. Lewis building, part of the Weatherhead School of Management, is a unique conglomeration of undulating surfaces and highly sculptural forms. With natural daylight in every room and a layout that facilitates unplanned interaction between faculty and students, the building itself not only defies convention, it also encourages students to do the same.
"We're trying to generate a new way of looking at business functions and help the students find a new way of looking at business mechanisms," says Gerhard Meyer, project manager for Gehry Partners, of Santa Monica, Calif.
"It was designed inside-out to enhance students' learning," adds Jeff Bendix, senior media relations representative for CWRU, hailing it as Cleveland's next architectural landmark.
Mayer explains that part of the building's uniqueness is its sculptural space, achieved by enclosing the exterior with metal and enclosing the interior with three-dimensional-shaped plaster. The interior contractor on the job was the GQ Contracting Co., of Cleveland.
"GQ has been involved in this building since before the contract was let," says Mayer. "They gave advice on how the design could be achieved economically."
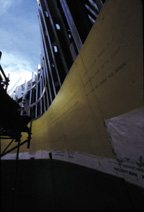
Hard eight
Make that achieved at all.GQ hard bid the job based on concepts yet to be proven. Once the job was awarded, it would be an additional eight months of research and development and familiarizing themselves with CATIA before the final framing design was complete.
"It is an extremely difficult framing job," says Ed Sellers, chief of operations and project manager on the building. "There are 200,000 square feet of curved and undulating surfaces with an uncountable number of shapes--no two alike. We figured out how to frame this job sitting in front of a computer. It was the combination of my field knowledge of conventional framing and CATIA modeling that allowed us to figure out how to frame this building.
"In these interior surfaces, studs are fanning and they create cylinders and cones," continues Sellers. "The wall doesn't appear to have a severe twist in short distance, but in long plane you can see the undulation. This is where we integrate studs with our corner details. If you look at a surface and it is made up of isoparms, stick lines that are straight and as they come closer together and farther apart, you actually create these curves."
Once the building was framed on the computer, it was time to get to work. At the site, a surveyor was required for the setting of each stud in a 200,000-square-foot surface. Accuracy was the key.
"I have to be right on because all of the subcontractors are using CATIA to lay out their work," says Sellers. "If my framing systems aren't right on, someone else's work won't fit."
And, as with all jobs, production was also key.
"The trick to the job was to create systems that can duplicate the (virtual) surface in the CATIA model and be field friendly for labor costs," he says. "We've done that."
As the job progressed, GQ saw the innovations it had created working with the computer actually realized in the field. One of the innovations was a new type of stud used for the more extreme curves. Traditional metal stud and track benders were not up to the task. The options were to use structural tube steel, which was extremely expensive, or to come up with something new.
"We have to create the actual shape," says Sellers. "When you bend a stud, you have segments; we needed a true curve. We've come up with systems that actually cut to match the surface."
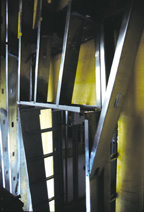
Ruffled frames
Another challenge would be the framing of the ceilings. The main atrium's ceilings roll and cascade over the building's four-story open atrium and others undulate and twist to create shapes much like giant potato chips. For this, GQ designed a custom carrier system that utilized conventional framing members. An actual full-scale mock up of this system was built in an abandoned warehouse, in order to prove the viability of this system.It could be said that the entire project broke new ground for the wall and ceiling contractor.
"Typically, a sub doesn't deal with an architect direct," says Sellers. "This project has allowed us to open up concepts and engineer systems and apply them. Our opinion is that the architect comes up with a design and needs us to make it reality. They want a surface and we are able to create what they have on their computer."
"If you look at the buildings that we are doing, everyone has a lot of responsibility and it can't be done without a collective effort," says Mayer. "You need the resources of everybody on the team to basically build something as complex as we have on the building. Everything there is to learn about how something like that can be built, which is very rewarding in the end."
But the building promises to be more at its completion, slated for summer 2002.
"What Frank personally says is that he wants the building to have an emotional reaction to the users," says Mayer. "He wants them to relate to it on an emotional level. And it does that."
"He hopes it will start fights in bars," adds CWRU's Bendix. "When it's done, you'll see why."