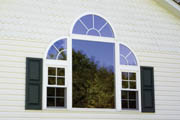

When homeowners discover that their insurance won’t pay for the escalating repair costs, they turn to the window installation companies to pay for the damage caused by the poor or improper installation.

Avoid like the plague
How should contractors protect themselves against situations like this? The first step is to arrange for training on proper installation methods—even for those who have been installing windows for decades—because new building methods often dictate changes in current methods and techniques.Most reputable manufacturers offer product training courses, in addition to those offered by industry organizations such as AAMA and WDMA. Having independent certification illustrates a company’s initiative and gives it greater credibility with homeowners. An equally important second step is to ensure that installers use what they’ve learned. What good is training if it isn’t applied on the job?
In an effective training program, installers learn what constitutes a professional installation. Typically, the four basic guidelines that every window installer needs to follow are:
1. Apply all flashings from the bottom up. Begin at the sill area, then apply the jamb or side flashing (overlapping the sill by at least 1 inch). Finish with the head flashings, again being certain that they overlap the jambs by at least 1 inch.
2. Seal overlapping joints with a premium-quality sealant to prevent wind from forcing water behind the joints. Although everyone knows that water runs down hill, you should also know that it can be forced to flow sideways—or even uphill—by strong winds.
3. Be certain that all sealants are compatible with surrounding materials. To test compatibility, take a sample of each of the materials and place a 3-inch piece of masking tape on each. Apply a bead of sealant directly over the tape and continue down over the surface of the material at least 6 inches. Tool the sealant with a blunt object to create a good bond, and allow the sealant to cure properly. Then pull the tape away from the surface at a 90-degree angle. A compatible sealant will tear within itself and stay adhered to the raw material.
4. Use only non-corrosive fasteners—preferably stainless steel—that are compatible with surrounding materials. Size the anchor to engage the structural materials around the opening by at least 1 inch.
Follow these basic steps to ensure a quality installation—but a professional will take it even further. A true professional understands that a good install begins with a good measure. Unfortunately, many home improvement companies assign this crucial task to a salesman or another individual who is not qualified to properly access and measure an opening. Inaccurate measuring can create tremendous problems for even well-trained installers, and result in delays, cost overruns and corner cutting—as well as leaking around the windows.
A “measure person” must understand many variables in home construction. Each of these variables will affect the correct point of measure. To measure properly, one must be able to identify the type of wall, the material the new window will anchor to, the position of the primary weather barrier of the home and the types of trim parts, flashing and sealants that will be required. A qualified measuring person also needs to understand construction and be able to identify decayed or damaged structural headers, jambs and sills for replacement.
Most importantly, this individual must know when to ask for help. For instance, if an opening needs to be altered, such as enlarging it for bow, bay or specialty-shaped window, a professional engineer or architect may need to be involved.
As a general guideline, the new window should be at least 1/4-inch smaller than the opening. In some cases, such as very large openings or openings that are more than 1/8-inch out-of-square, additional allowances must be made. Leave as much clearance as necessary to allow the new window to be set square, level and plumb; never fit the new window tight to the opening.
Once a qualified individual has measured the openings, the installer’s job begins. Windows have become increasingly specialized, so a good installer will take measures to become knowledgeable about the type of products he’s installing. The material a window is constructed of, such as aluminum, wood, fiberglass or vinyl, and its design will dictate the type of flashing methods and anchors that should be used. Many window types require the use of a sill pan, a custom-made aluminum or composite pan that is formed to fit the opening’s sill. The sill pan is integrated into the flashing to collect and drain excess water away from a home’s structural components.
Windows are outfitted for various means of attachment. These include block-framed products, mid-mounted finned products and externally mounted finned products. It is crucial that a professional installer understands the limitations of each window and the type of mounting it utilizes. Fins can be integrally extruded to the frame or come as separate parts that are factory-applied, field-applied or folded out. In some instances, fins are structural—or load bearing—and in others they’re non-structural. If fins are not waterproof, they will require rigid head flashing (extra field flashing at the head) to create a watertight joint. If in doubt, always ask the manufacturer.
Once an installer has selected the appropriate fastener, the key question becomes, “Where should the fasteners be placed?” In most instances, manufacturers suggest that the installer apply anchors every 16 to 18 inches around the perimeter of the window, using a minimum of three anchors per side. All fasteners used at the sill need to be sealed to prevent water penetration into the wall cavity.
Shimming material should be used at every anchor point. Wood shims or any wedge-type shim should always be used in pairs. Although wood wedge shims are the most common, plastic shims are a better choice, especially at the sill because plastic won’t absorb water or compress. Also use additional shims and anchors at all lock and hinge locations.

Twisted and racked
Another important point is that new windows need to be square, plumb, level and flat throughout the anchoring process. Most individuals understand “square, plumb and level,” but may not know what “flat” means. Windows can be racked or twisted within the opening—or that the original opening itself may be twisted. If an installer doesn’t ensure that the new window is flat, it will lead to poor operation, early failure—and unhappy homeowners. To ensure flatness, stretch two pieces of string diagonally across the interior of the frame; the strings should just lightly touch in the center. These can be taped to the frame and left to act as a guide throughout the shimming and anchoring process.Contractors also need to be aware of ever-changing building codes. New codes are being adopted throughout the country, as federal and state legislators deem them reasonable. First, if building codes are involved, inspectors must be notified to approve window installations based on thermal efficiency, design pressures, mullion deflections and possibly even impact protection performance. Required new inspections add further complexity to the window industry because installers now have to understand how window ratings are achieved as well as the meaning of each value.
Another recent development is that many utilities now offer rebates for energy-efficient products. Consumers must purchase windows that meet stringent requirements to qualify for these funds. This is important to the window installer because, in order to collect this money, many companies mandate that the homeowner present the window’s label, which often are unknowingly discarded by the installer. Collect these labels and leave them with the homeowner once the job is complete—not only for energy rebates, but also for the care and cleaning information often printed on them.
Lastly, there is one very important element that sets professionals apart from the rest—respect for the customer’s home! Installers need to protect the homeowners’ belongings from possible damage during installation and be certain to leave the job site clean. Keep appearances neat and professional because installers represent the company contracted to do the work – and they form the impression homeowners have of the company. It makes very good business sense that the impression left is a professional one.