The Straight Scoop on Curves

We've been there before. The architect has created a great looking interior and has drawn lots of curves into the design. The owner loves it. The subcontractor loves getting the job. But he's a little worried about his crew's ability to handle all of those curves. Framing and finishing curves so they become an architectural statement rather than an embarrassment is critically important. After all, the subcontractor's reputation and future business with the architect is on the line. Everyone wants the work to be done right. And the subcontractor wants to make some kind of a reasonable profit, too.

Such an example is Green Country Interiors, of Tulsa, Okla., the subcontractor that used more than 11,000 linear feet of hand-curveable track on the Cherokee Hotel and Casino, in Tulsa.
Green Country decided to use Flex-C Trac as opposed to the traditional method of "cutting and snipping" for various reasons but mostly due to the time/labor savings. The cutting and snipping method can take upwards of 20 to 30 minutes per 10-foot piece. By using the flexible track product, the subcontractor's labor was cut down to as little as five minutes per 10-foot piece. Since labor is one of the major expenses, it is encouraged that contractors compare overall costs of both methods.

Task at hand
"The project was demanding," says Billy Tobey, vice president and general manager of Green Country Interiors, commenting on the Cherokee Hotel and Casino. "We were challenged to find a way to save money without sacrificing the integrity of the final appearance."This hotel has an elaborate interior that was designed to look and feel like Las Vegas. The interior design features traditional Cherokee symbols and incorporates art deco in its styling (this architectural movement is common in Tulsa). The seven-story hotel includes 80,000 square feet of gaming space. Its floorplan features numerous curved soffits and theme elements that rely heavily on compound radiuses.
The company was faced with day-to-day design modifications that had to be accommodated within an already-tight schedule. The first hurdle the subcontractor had to overcome was the design and value engineering process. The original basic set of drawings was found to be incomplete in the area of details. Challenged to find a way to not incur additional costs, yet not compromise the integrity of the original plans, Green Country was able to meet the demands of day-to-day modifications to the framing. With a job that included several varying curves, radiuses and integrated themes, the foremen of the company were heavily relied on to display their "know-how" to achieve the set goals of the jobs, working closely with the General Contractor Flintco Cos.
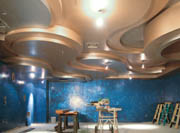
Another reason the subcontractor used hand curveable track was to help create the best-looking finished product. Since curves are often the focal point of the building, it's good when the subcontractor can meet and exceed the expectations of the architect and owner. When tapers and finishers are given a smooth curved surface on which to apply their mud, they usually return the favor and make everyone proud.
If you read this article, please circle number 336.
Looking for a reprint of this article?
From high-res PDFs to custom plaques, order your copy today!