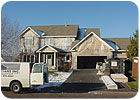
A recent remediation of a one coat stucco home near St. Paul, Minn., reveals some interesting traits that on the surface may suggest summer solar radiation induced water vapor transport through the stucco, water-resistive barrier and oriented strand board sheathing.
WUFI is an acronym for "Wärme und Feuchte Instationär." What's that? In English it means "transient heat and moisture transport." Does that make more sense? How about this: WUFI is a two-dimensional transient wall system hygrothermal simulation program.
OK, before you put this down and move on to something you think is more important, hear me out.
WUFI is important because it was recently used to sort the wheat from the chaff on some of the moisture intrusion debate on stucco walls. You remember stucco: That simple natural earthen material that we have been using to clad our walls for thousands of years. Suddenly, this low maintenance premium siding, known for its ability to resist the affects of water, air and fire, has come under scrutiny as a bane for moisture intrusion issues. What seems to be overlooked by its critics is that stucco is as natural a building product as stone, wood and brick. It was and continues to be the original "green" building product. When we start to question the viability of such a product's use, it is time to apply the brakes and take an informed look at the direction our building practices are taking us.

Transparent sheet plastic drapes the water damaged oriented strand board sheathing that was exposed after the stucco was removed on the south elevation. Could this be caused by summer solar radiation induced water vapor transport from the outside?
Reservoir dogs
In the plastering industry, we had just become accustomed to "barrier" cladding entering the vernacular. Now comes the concept of "reservoir" cladding. What does this mean? Some claddings act as reservoirs and store water. This interesting concept is not lost on all of us who have always thought of "reservoirs" as great storage basins that hold water. Having lived in and visited various parts of the country I take this reference as akin to great holding ponds, such as Lake Lanier in Georgia, Lake Mead in Nevada and the Edwards Aquifer in Texas. I guess that is why it is difficult for me to equate stucco with any kind of reservoir (it doesn't seem to hold water). But that is what this term conjures up. Other known "reservoir claddings" include concrete block, cedar siding and brick.Alas, in the context of this article, one issue that has become a persistent theme laid out by credible scientists and engineers is that "reservoir" claddings (stucco in particular) are prone to condensation-related failures produced by summer solar radiation induced water vapor transport. The long and short of what this means is that stucco soaks up wind driven rain; then through a process of the sun hitting the surface, it vaporizes and diffuses through the composite exterior wall and finally condenses on the back side of the vapor retarder. This is exacerbated by physics, which maintains that high vapor pressure (exterior summer conditions) seeks low vapor pressure (interior air conditioned space).
For those of you unaccustomed to vapor retarders, this is generally constituted as a piece of 4 to 6 mil polyethylene plastic installed over the framing before the drywall is put into place. Their purpose is to thwart interior water vapor created in the winter months from cooking, bathing, washing clothes, etc., from entering the building envelope and condensing on the cold interior surface of the wall sheathing. The question then, is whether this vapor retarder is creating a dam in the summer months that prevents inward drying potential and contributes to moisture related problems.
By 2003, the Minnesota Lath and Plaster Bureau had heard enough of the speculation to be concerned. In April of that year, the bureau contracted with the University of Minnesota Building Physics and Foundations Research Program to investigate this issue. This is where the term WUFI originates. It is a computer simulation-modeling program which gives a two-dimensional snapshot of a wall system's moisture vapor performance, given various imposed climate conditions on the model.
Considering the sophistication of what we are discussing, this type of computer modeling remains rather basic in terms of what it can and cannot accomplish. This is because the WUFI methodology only describes the movement of water vapor driven by vapor pressure and the movement of liquid water driven by capillary flow. WUFI is also exceptionally dependent on laboratory measured material properties and this is perhaps the greatest challenge in its use. For these reasons, all the simulations were performed with wind-driven rain on the exterior stucco surface being the only source of water. Other sources of water, such as air movement, gravity and rough opening runoff onto the water-resistive barrier, were not measured.

The north exposed wall with the sheathing being removed identifies rot to the exterior face of the studs but not on the interior face of the studs. This effectively rules out condensation on the exterior side of the vapor retarder imposed by summer solar radiation induced water vapor transport. Other possible scenarios to this mystery include wind-driven rain bypassing the stucco and water resistive barrier at the perimeter or through cracks; or perhaps condensation in the winter of water vapor from inside the house onto the interior side of the sheathing.
What was tested
In the first phase of the simulations, six variations of a typical stucco wall system were researched based upon published material data properties from American Society of Heating Refrigerating and Air-Conditioning Engineers and National Institute of Standards and Technology. This included 20 additional variations of the wall systems with various sundry changes in insulation materials, water-resistive barriers and interior vapor retarders. In the second phase of the simulations, a third set of published material properties were utilized from National Research Council (Canada) and other claddings, including brick, cedar, cement board and vinyl siding, were investigated.Keeping this in perspective, we were interested in viewing the response of these materials relative to each other in a Minnesota climate. In this context, the Phase I simulations included six different interior and exterior conditions and in Phase II , two additional climate variations were added. What insight the simulations could investigate then were the answers to the following questions:
- What are the moisture responses of standard code compliant stucco wall systems to the rigors of Minnesota temperature swings, relative humidity and rainfall?
- Given negative moisture responses, can standard code compliant materials be engineered to be more fault tolerant?
- Can non-standard materials with a broad range of properties be used to successfully engineer a fault tolerant stucco wall system?

The north exposed wall expresses a distinct pattern in relation to the roof plane, a cathedral ceiling and closet behind the exterior wall.
BACK TO SCHOOL
What was immediately apparent, in Phase I of the project, was that success or failure is very sensitive to the composite material properties (ASHRAE, NIST) and details of the wall configuration.For instance, using ASHRAE material data, a typical Minnesota configuration of a framed wall system with 5/8-inch ligno-cellulosic fiberboard (Bildrite), two layers of Grade D building paper and stucco revealed marginal stability for the wetting/drying cycle of the sheathing. There was also condensation on the fiberglass insulation and excess water content on the polyethylene vapor retarder. The results even bore out worse when oriented strand board was used in the configuration in lieu of the fiberboard. These issues were amplified even more when the material data was switched from ASHRAE to NIST.
During the testing process, our principal investigator, Louise Goldberg Ph.D., learned of a newer property database that had become available from the NRC of Canada. With this information in hand, Dr. Goldberg ran the more relevant simulations a third time.
This time around the results were dramatically different than those in the Phase I simulations. A comparative chart in the report reveals that where there were concerns for the stability of the wetting and drying cycle of the fiberboard sheathing in Phase I, the same concern did not exist in the Phase II simulations. Similarly, condensation on fiberglass insulation and excess water content on the vapor retarder did not appear to be an issue in the second phase simulations.
These startlingly different findings from the first phase of the project to the second phase, perhaps, overshadows the knowledge that had been gained by the project as a whole. However, what can be concluded by these contrasts in outcomes is the sensitivity of the simulation program and the expressed differences that resulted from ASHRAE, NIST and NRC property databases.
According to Dr. Goldberg, the NRC property data "gives a clear alternative view of the simulated performance of stucco-clad wall systems with a consistently measured set of material properties." While Dr. Goldberg refrained from passing judgment on the accuracy of any particular set of material properties, she noted that "... perhaps the Phase II material properties are superior to those of the Phase I and hence, in absolute terms only, may be closer to reality."
Final Thoughts
The WUFI program can be construed as a simple tool in the investigation of a complex issue. What is gained by this research is the knowledge that depending upon the properties of the materials used and in the presence of exterior bulk water only, solar radiation induced vapor transport does not necessarily pose a serious threat to moisture related problems in conventional stucco due to condensation.The broader issue of moisture intrusion by other more complex physics is more challenging and systematic research of the issues that we are confronted with continues to be warranted.For now, our research provides a resource for suggesting some changes that will make stucco wall systems more fault tolerant even within the constraints of current building practice.
sidebar:
FURTHER FINDINGS
Phase I FindingsPhase I of the research reveals the impact that subtle variations in the composite wall materials can have on the wall system as a whole and demonstrated the full range of vapor-sourced, stucco wall system failures. Even with its inherent limitations, the Phase 1 research demonstrates the importance of having wall systems that can be constructed to be fault tolerant.
One such system that Dr. Goldberg identified as "bulletproof" was a wall composed of (from inside to outside): acrylic paint, 1/2-inch drywall, closed cell polyurethane insulation in a 2x6 stud frame, fiberboard with two layers of Grade D building paper and stucco.
Another option that was determined to be more cost economical was a composite of: acrylic paint, 1/2-inch drywall, a smart vapor retarder, unfaced fiberglass batts in a 2x4 stud frame, 2 inches of extruded polystyrene, fiberboard, two layers of Grade D building paper and stucco.
Phase II Findings
With a different set of material properties from those used in Phase I, the Phase II simulations indicate vapor transport does not produce condensation related failures under the same interior and exterior climate conditions used in Phase I. This finding includes the current practice of installing a warm-side polyethylene vapor retarder. This is in contrast to the many anecdotal conclusions that have been reached by forensic engineers, experts, and in some cases, those that have added this explanation to their repertoire, inadvertently or otherwise denigrating the reputation of stucco.
What is perhaps most revealing is the fallibility of the building code in providing simplistic requirements to complex issues. Stucco wall systems that include variables, such as different sheathings and water-barriers, need to be thought out systematically rather than by "one-size-fits-all" descriptors.
Other Key Findings
- Alternate claddings, such as vinyl and wood siding, are shown to yield acceptable hygrothermal performance.
- WUFI is not applicable to brick claddings where free surface water and air movement are contributing factors.