Palm Down

The joke within the global construction industry has been that Dubai’s national flag would feature a landscape sprinkled with cranes. And anyone who has looked at a picture of the city over the last five years knows it’s been the busiest construction site in the world. Destined to be a world-class city, Dubai certainly has worked hard to earn this stature. Among one of the hotspots in this growing city is Atlantis, The Palm. This high-scale hotel is an oasis for the rich and famous.
Construction of The Palm faced many unique and difficult challenges during its production schedule. The project is located on a manmade island in the middle of the Persian Gulf-which means that there is very little space available for job site operations.
In addition, the January 2008 “Green Building” initiative of His Highness Sheikh Mohammed bin Rashid Al Maktoum, vice president and prime minister of UAE and Ruler of Dubai, makes it mandatory for all new construction in Dubai to adhere to international green building specifications.
The Palm is the brainchild of Sol Kerzner and the sister hotel of the Atlantis, Paradise Island in the Bahamas. The Palm is the flagship resort on The Palm Jumeirah, a 46-hectare (115 acre) man-made island in Dubai. Built in just 31 months, this 1,539-room resort hotel-the gateway to a mega-entertainment destination that includes 17 hectares (42 acres) of water-themed amusement, an endless stretch of beach, luxury boutiques, restaurants, a nightclub, spa and more-opened in September 2008. To achieve this feat, numerous construction challenges had to be overcome. BASF Construction Chemicals provided products and support to meet the challenges.
“Kerzner International, the project developer of Atlantis, The Palm, faced a number of constraints,” says Julian Pritchard, regional sales manager of BASF. “On a manmade island in the middle of the gulf, there is very little space for site operations. Construction materials also have to withstand the rigors of sea and desert environments. A shortage of skilled and unskilled labor, the result of the construction boom in Dubai, needed to be taken into consideration, as did the 1.5 percent escalation in construction costs per month.”

In keeping with green building design principles, the exteriors of the buildings at the resort needed to be insulated from extreme heat to increase the energy efficiency of cooling systems. This would translate into not only lowered energy expenditure but lower CO2 emissions and pollution.
The Senergy EIFS line, a brand of BASF Wall Systems, was proposed for the 95,000 square meters of external façade of the Royal Tower Hotel at Atlantis, The Palm. Its effectiveness as an insulator and weather barrier, and its highly flexible aesthetic properties, enabled BASF to offer design options for the whole project.
For the Royal Tower Hotel, it was the Senerflex finish coat that was used, delivering an exterior that is a testament to the aesthetics and functionality of the product.
Sonolastic NP2, a multi-component polyurethane sealant by BASF, was used for all expansion joints in the balcony. One key advantage of Sonolastic NP2 is that it can be matched with the color of the external façade.
The project also gave BASF the opportunity to demonstrate the capabilities of its Mastertile range of adhesives and grouts.
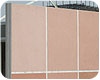
At the Royal Towers inside the resort, prefabricated bathroom pods were designed in an effort to lower demand on human resources and fast track construction. Each bathroom pod-3.5 metric tons of marble sink, bathtub, shower, lavatory, bidet, taps and tiling-was swung by crane onto a slab and slid into place.
Modular by Al Naboodah Laing O’Rourke was appointed as the subcontractor to assemble the bath pods to pre-specified standards and transport them to the site. Waterproofing these bath pods and finding a specialized solution to affix the tiles-one that could withstand the 20 kilometer journey to the site-were primary challenges for Modular.
BASF proposed the use of its Mastertile solutions for waterproofing the entire pod and fixing the tiles.
The Mastertile system consists of a two-component polymer modified tile adhesive (Mastertile 30/Mastertile 200) and a waterproof flexible protective coating (PCI Lastogum) especially developed to be applied under ceramic coverings in wet areas like showers and bathrooms.
THE NEED OF THE HOUR
There were numerous benefits in using an offsite facility for the project developers. Efficient sub-assembly operations shortened factory fit-out time, resulting in a 900 man reduction of onsite labor. Construction processes were standardized and materials handling processes mechanized. Savings on preliminaries including-reduced material storage logistics, less waste generated, minimal re-work and reduced general supervision could also be achieved. Assembling the bath pods offsite also meant that the health and safety standards could also be improved.
The Dubai government’s call for action on energy conserving building practices has been based on the need to address the ever-growing energy consumption in the region. Rising living standards and greater use of cooling systems means the demand will continue to grow. W&C
Looking for a reprint of this article?
From high-res PDFs to custom plaques, order your copy today!