Is It Really a Leak?
The
waterproofing system is not always at blame when
it comes to a leak in the building.

When it comes to thermal insulation and weatherproofing there are many factors involved, and it is not easy to point fingers to see who is going to pay for the bill in a leaky building. Sometimes, the waterproofing system has been blamed for any type of leak related issues. But the fact that water is manifested in the interior of the building is not always due to a lack of detail or design in the waterproofing system.
Water can manifest in the interior walls when the temperature drops below dew point or when vapor pressure rises above saturated vapor pressure at a given temperature. When this process is visible to building occupants, it is called condensation.
Surface
condensation is the process whereby water is deposited from air containing
water vapor. For this to occur, factors like temperature and moisture content
need to occur at the same moment. Surface condensation is not only associated
with cold or humid climates, it can manifest at room temperatures as high as 60
degrees Fahrenheit (if the room temperature drops from 80 degrees Fahrenheit at
50 percent relative humidity, for example). Therefore, it may happen in any
project when the wall’s thermal behavior has been overlooked or not designed
properly. On other occasions, the thermal behavior has been addressed but
interfaces between adjacent systems were not analyzed.
Another area to look closely at are systems transitions. The transitions’ response to a bad design will be condensation in the first place; but problems related to severe heat loss can also occur. This phenomenon receives the name of thermal bridge.
Thermal bridges occur when two different materials with relatively high thermal conductivity differential are installed next to each other, or when a single member is exposed to a high temperature differential (single curtain wall framing members that are exposed to the exterior and interior of the building with no thermal break or treatment, are a good example of this).

If there is a potential issue, surface condensation is going to be visually evident during the building’s service life. But there is another type of condensation that generally is not so evident and can occur between the wall layers. I am referring to interstitial condensation. This type of condensation works on the same principle of material temperature and dew point (but it involves many more factors since it depends on materials resistance and interfaces behavior between them).
Interstitial
condensation can become a problem if the wall’s air cavity is too small to
allow some air movement or if thermal insulation is insufficient to prevent
heat loss. The problem is that it can take several years before we notice the
problem. Draining the cavity is also very important, as well as moving this
drained water, in a controlled manner away from the
building.
Determining if you need to check the thermal behavior of your project is not complicated. Remember that all projects and building functions are very different from each other. It can be said that if your project is in a relatively stable climate with a constant temperature all day long, with a relatively low humidity, little or no artificial-ventilation or no vegetation around, and with the perfect cladding system, then and only then your project could behave fine, thermally speaking. Even if all these factors are met, there is a chance that in the near future, the building use or the climate will vary, and then the problems could arise.

The illustrations in this feature show some thermal analyses performed on several types of cladding systems. All of the images shown are for illustration purposes only and do not represent any particular solution.
The
detail shown in Illustration 1 is the transition between a curtain wall sill
and a terracotta (masonry) system. This model was built to determine the
surface temperature on the materials and investigate the potential for surface
condensation. Right below the curtain wall frame, the temperature is 45.2
degrees Fahrenheit. If the interior dew point temperature was equal or higher
than this value, then, condensation will occur. On the other hand, if the
interior dew point temperature is 37 degrees Fahrenheit, for example, then
there is no condensation problem.
Even with the temperature gradient shown in the illustrations, some of the wall elements can appear to be below dew point. It does not mean that condensation will occur since the scope of these models is to show surface temperature only. For interstitial condensation, there is another type of calculation.
For
Illustration 2, it can be seen that the inside temperature is relatively low
due to the lack of protection from the outside environment. There is only a
thin metal cap at the underside of the framing member. Due to this, cold
temperature is drawn towards the inside of the building. It is most likely that
surface condensation will form along this entire framing member, unless the
detail is modified or thermally improved.
Making changes to a wall in order to improve its thermal behavior is sometimes inexpensive and can save thousands of dollars in repairs, if detected and addressed before construction. Hence, it is greatly encouraged to review the thermal behavior of walls for every project and if possible for every detail in the building envelope system.
The next time you see water inside your building, think twice before tearing off your interior finishes trying to find the source of the leak; there is a chance its source is not water infiltration and you will end up paying to repair your finishes. Also, before looking for the contact information of the “responsible” contractor and calling them for a repair, there are many factors related to thermal behavior that need to be evaluated to confirm the cause. The problem sometimes lies in the design. There are many inexpensive alternatives to resolve this problem without having to completely refurbish your building. So next time, ask yourself the following: Is it really a leak?

This and the next two pictures show condensation accumulation on the glass’ inside
surface. This is very common in
monolithic glass applications used in the past.
When it comes to thermal insulation and weatherproofing there are many factors involved, and it is not easy to point fingers to see who is going to pay for the bill in a leaky building. Sometimes, the waterproofing system has been blamed for any type of leak related issues. But the fact that water is manifested in the interior of the building is not always due to a lack of detail or design in the waterproofing system.
Water can manifest in the interior walls when the temperature drops below dew point or when vapor pressure rises above saturated vapor pressure at a given temperature. When this process is visible to building occupants, it is called condensation.

This and the following two pictures show condensation accumulation on the glass’ inside
surface. This is very common in
monolithic glass applications used in the past.
Another area to look closely at are systems transitions. The transitions’ response to a bad design will be condensation in the first place; but problems related to severe heat loss can also occur. This phenomenon receives the name of thermal bridge.
Thermal bridges occur when two different materials with relatively high thermal conductivity differential are installed next to each other, or when a single member is exposed to a high temperature differential (single curtain wall framing members that are exposed to the exterior and interior of the building with no thermal break or treatment, are a good example of this).

Condensation Consequences
Consequences from condensation are well known within the industry such as: mold growth, dampness, wall paper peeling, insulation decay, corrosion, pattern staining, etc. The good news is that these issues can be minimized if the system’s thermal behavior is checked or modeled. This way, any potential problem can be addressed. The technology now exists, where with accuracy and precision the condensation issues and thermal bridging can be predicted and avoided. And generally, this engineering cost cannot even be compared with the cost of having to repair a problem caused by these factors.If there is a potential issue, surface condensation is going to be visually evident during the building’s service life. But there is another type of condensation that generally is not so evident and can occur between the wall layers. I am referring to interstitial condensation. This type of condensation works on the same principle of material temperature and dew point (but it involves many more factors since it depends on materials resistance and interfaces behavior between them).

Determining if you need to check the thermal behavior of your project is not complicated. Remember that all projects and building functions are very different from each other. It can be said that if your project is in a relatively stable climate with a constant temperature all day long, with a relatively low humidity, little or no artificial-ventilation or no vegetation around, and with the perfect cladding system, then and only then your project could behave fine, thermally speaking. Even if all these factors are met, there is a chance that in the near future, the building use or the climate will vary, and then the problems could arise.

Illustration
1
What Needs to Be Done?
A good start is always to define the wall construction, the wall elements and the arrangement of the elements within, and then run a thermal analysis. After this analysis, and depending on the results, thermal bridging must be eliminated. An optimum size and efficiency should be chosen for the insulation, and perhaps, lower the vapor pressure inside the building. Each of these solutions has several options and they are system dependant.The illustrations in this feature show some thermal analyses performed on several types of cladding systems. All of the images shown are for illustration purposes only and do not represent any particular solution.
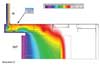
Illustration
2
Even with the temperature gradient shown in the illustrations, some of the wall elements can appear to be below dew point. It does not mean that condensation will occur since the scope of these models is to show surface temperature only. For interstitial condensation, there is another type of calculation.

Constant
condensation might damage adjacent materials, and depending on the frequency,
it might even cause corrosion of metal.
Making changes to a wall in order to improve its thermal behavior is sometimes inexpensive and can save thousands of dollars in repairs, if detected and addressed before construction. Hence, it is greatly encouraged to review the thermal behavior of walls for every project and if possible for every detail in the building envelope system.
The next time you see water inside your building, think twice before tearing off your interior finishes trying to find the source of the leak; there is a chance its source is not water infiltration and you will end up paying to repair your finishes. Also, before looking for the contact information of the “responsible” contractor and calling them for a repair, there are many factors related to thermal behavior that need to be evaluated to confirm the cause. The problem sometimes lies in the design. There are many inexpensive alternatives to resolve this problem without having to completely refurbish your building. So next time, ask yourself the following: Is it really a leak?
Looking for a reprint of this article?
From high-res PDFs to custom plaques, order your copy today!