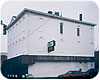
This picture and the next are a before and after example of an old
building that was redone with an EIFS finish that looks like brick. What a
difference. Photo courtesy of Dryvit Systems.
I often get calls from people wanting to “beef up” the performance of their EIFS walls. There are some things you can do to improve performance and this month’s column has a potpourri of strategies for common problems.
Impact Resistance
Since in most wall areas the EIFS is never in contact with hard objects that can cause dents and holes, the use of standard grades of EIFS with light reinforcing mesh works just fine. During the phase of designing the façade, areas that need extra reinforcement can be identified and those areas can be beefed up using heavy reinforcing mesh. Wall areas that fall into this category include the bottom of the wall near grade and sidewalks, and around windows where window washers and maintenance staff may be working. Sometimes, this extra level of reinforcement is simply not enough or is never installed. Is it possible to retrofit an existing EIFS to improve its resistance to impact damage? Yes. There are several ways.One way is to add extra layers of mesh on top of the existing EIFS lamina. This is done by first filling in the existing EIFS finish with adhesive, and then adding additional layers of basecoat adhesive, mesh and finish. The existing finish needs to be clean and the texture of the finish is filled with basecoat adhesive to make it smooth. Usually, a noncementitious adhesive is used. The additional layer can be installed only where needed but has to be done carefully, lest the increased thickness in the new areas become visible.
A non-EIFS solution is to keep hard objects from coming into contact with the EIFS in the first place. This is usually done by placing barriers next to the EIFS. Pipes filled with concrete, and embedded in driveways, are used near truck doors. Heavy metal angles that protrude from the lower horizontal edge of a wall near a sidewalk can keep people and shopping carts away from the wall. Shrubbery can be used on grade to keep lawnmowers and snow plows away.

Changing the Texture
The texture of an EIFS finish can be changed. The trick is to fill in the existing texture to make it smooth, and then apply the new finish; it’s hard to get a consistent texture when applying one-textured coating over another. Usually, a noncementitious basecoat adhesive is used to fill in the texture.Insulation Level
Although EIFS is highly energy efficient, sometimes even more insulation is desired. If the supporting wall is hollow (i.e., stud framing), additional insulation can be added from indoors. Likewise, insulation can be added on top of the interior finish but this requires dealing with electrical fixtures, ducts and doors, and also takes up floor space.Adding more EIFS on the outside is possible and it doesn’t interfere with the ongoing use of the building. New EIFS insulation, basecoat and finish can be glued onto the face of the EIFS. Attention needs to be paid to the edge of the EIFS, where there are openings and where there are objects projecting through the EIFS.
Roof Insulation
Although EIFS is an energy efficient wall cladding, if the objective is to save more energy, the roof should be considered too-not just the walls. This is especially true on large, single-story windowless buildings such as warehouses, where the majority of the heat loss or gain is actually through the roof, not the walls.Air Leaks
EIFS is seamless and air does not seep through the coating. However, air can get around the edge of the EIFS if the perimeter is not sealed. Caulking does not last forever and maintaining the seal is simply a matter of checking the condition of the sealant-especially at windows and doors-and replacing areas that are worn out.Removing old sealant, without damaging the EIFS, needs to be done carefully so it does not damage the EIFS basecoat. The new sealant should be attached to the basecoat, not the finish. Solvents should not be used to remove old sealant, as some solvents can leech through the EIFS coating and dissolve the foam.
It may also be possible to apply new sealant over old. This can make for big, ugly joints but can save a lot of time and money. The old sealant should have a bond breaker material applied to it, so the new sealant does not stick to it. The use of preformed sealant strips, such as Dow Corning’s 1-2-3, are cost effective. They change the appearance of the joint from looking like an architectural joint to one similar to a batten.
Adding EIFS with Drainage
When the big news took place in the 1990s over water leakage that was supposedly caused by EIFS, the design of EIFS as a cladding system took a step forward. The building codes mandated adding drainage to EIFS, and EIFS producers responded by coming up with a number of ways of incorporating drainage. Basically, what the drainage system involved was putting a water resistive barrier over the wall sheathing, and then creating a cavity between the inside of the EIFS insulation and the WRB. This drainage capability was intended for use in new construction, not as an add-on. Nevertheless, people asked if drainage could be retrofitted onto an existing EIFS. The basic answer is no but it has been done-with difficulty.The problem is that EIFS cannot be disassembled and reused and the drainage system is buried in the EIFS. One way is to strip off the entire EIFS to the substrate, and install a whole new EIFS with drainage system. Needless to say, this is expensive and time consuming. An extenuating circumstance is the fact that the sheathing substrate usually gets ruined in the process of taking off the EIFS. Thus, it often needs to be replaced.
It is possible to put a new EIFS over an existing EIFS and incorporate the drainage capability in the new EIFS. The existing EIFS lamina can act as the WRB and the new EIFS uses grooved foam or a drainage matt to provide the drainage. A problem with this approach is it does not necessarily address the true source of most leak problems. The real culprit has been shown time and again to be the edge of the EIFS, particularly where there are flashings or caulking, or the lack thereof. Hence, the value of retrofitting drainage to an EIFS is sort of a waste of time compared to the benefits of carefully doing the details at the edge of the EIFS.
Slopes and Flashings
Speaking of flashing, it was common for many years to not use flashings at key places in EIFS, instead relying on caulking. Areas of particular concern include window heads and sills, parapets and penetrations, such as HVAC sleeves. Adding flashings that actually work to an existing EIFS is often difficult, as the flashing is normally attached to the substrate, and the presence of the EIFS makes it necessary to remove a band of EIFS, install the flashing and then rebuild the EIFS. This is expensive and often leaves visible repair patches. The same is true with windows, where there’s often not enough space to slip a flashing under a windowsill far enough to gather the water and actually do some good.As for shallow sloped areas, especially at sills, the only real way to increase the slope is to cut away the EIFS to increase the slope, and rebuild the EIFS.