The Power of Plaster
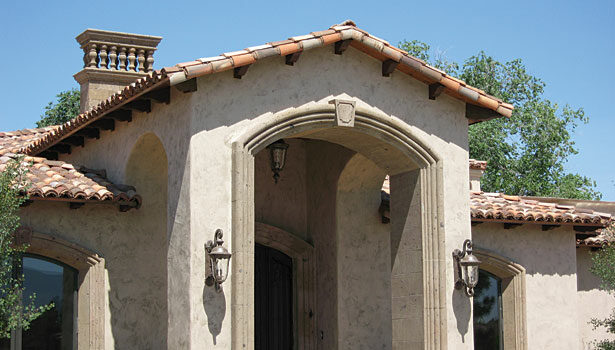
Aged "Tuscan"Â acylic finish, exterior.
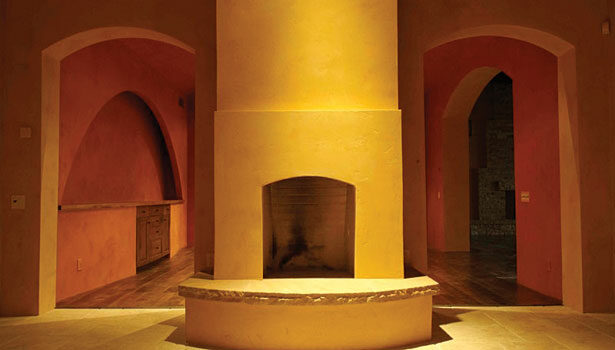
Multicolor interior acrylic “mudd” plaster.
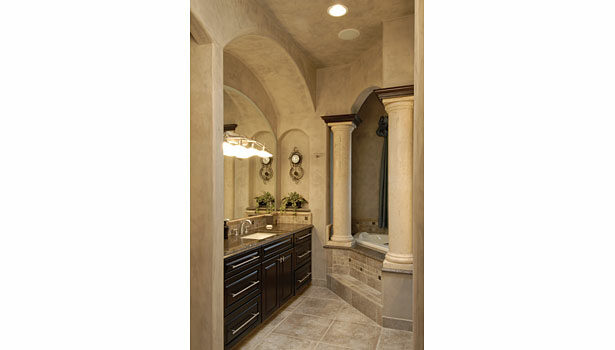
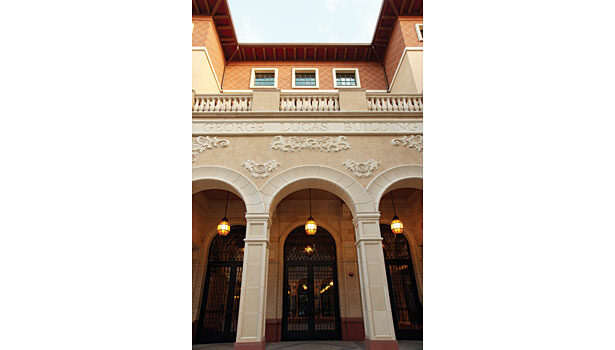
USC School of Cinematic Arts—different aesthetic affects, including Anciano finish.
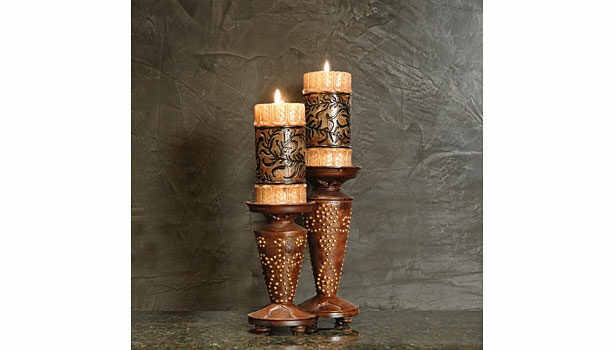
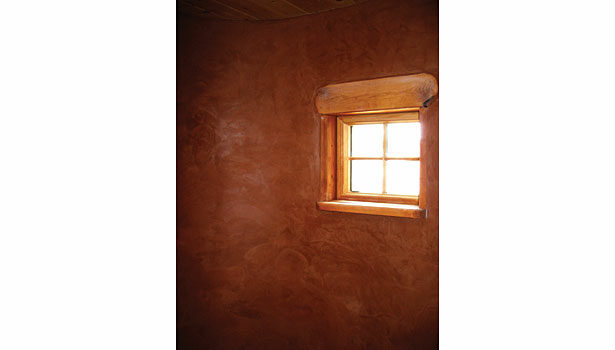
Adobe out building, polished acrylic earthen finish.






For thousands of years, plaster has been the medium of choice for protective finishing mortars, ornamental sculpting mortars and artistic reliefs. From Egyptian tombs to Greek artisan plaster castings, Middle Eastern geodesic dome homes to the cathedrals of Rome—plaster is renowned for its durability, aesthetic appeal and design versatility. Over the last five centuries, the advancement in both methods and materials has continued to advance its popularity, with today’s high-performance technologies infusing exciting new opportunity into the plastering industry.
THE EVOLUTION OF PLASTER
As the industry has evolved, so have the names used to associate plaster materials with various compositions, application styles, functions and branding strategies. The names, in and of themselves, do not consistently reflect function, intended use or performance. This lack of standardized nomenclature can lead to a vast difference in perception of what is being discussed or installed.
Gypsum, clay and limestone based plasters have traditionally been associated with interior applications, while sand and cement plasters have been associated with exteriors—all requiring significant time and labor to install. Venetian plaster is an American coined term which is the most often misrepresented. It refers to a specialized lime based aesthetic finishing plaster that is hand applied over a lime and sand based mortar in numerous, labor intensive steps, then burnished to a high polish or left unpolished to create a stone like finish. Today, Venetian plaster is often used to refer to a broad category of decorative finishes.
Innovations in gypsum and cement based plasters made their marks on the industry through the 20th century, along with advances in lath, with the introduction of rock lath, plasterboard, drywall and veneer blue board. The primary focus on reducing installation times and increasing productivity replaced ornate and dramatic aesthetic appeal. Post World War II, gypsum veneer plaster was developed to simulate a plaster-like surface and meet construction schedule demands, coinciding with the evolution of drywall to greatly reduce time to completion. These advancements afforded more project turns and increased profitability.
The introduction of synthetics during the Industrial Revolution afforded good bond performance to all types of wallboard, high strength, and durability, and once painted or colored, some aesthetic appeal. However, due to their UV and moisture sensitivity, use was limited to interior applications and made for difficult repair and maintenance.
The plaster industry saw a merging of materials and techniques in conjunction with advances in material technologies and performance as we entered the 21st century. This resulted in the creation of new, higher performing materials that achieve both performance and aesthetics and improved times to completion.
ADVANCEMENTS IN THE INDUSTRY
The introduction of acrylic polymers was a key advancement in finish materials, chiefly developed by the EIFS industry. These acrylic veneer plasters can be applied, both interior and exterior, to virtually any substrate without a bonding agent. Advancements in acrylic modified cement and lime based plasters increased abuse and impact resistance, cleanability and ease of repair, and have afforded a much broader range of integral color and texturing options.
Modern 100 percent acrylic based formulations now offer the best of all worlds—both performance and aesthetics. There are many advantages of these materials. They create very tough, durable surfaces with increased chip resistance, high tensile strength, exceptional hardness, abrasion and adhesion, good moisture resistance, and easy repair and maintenance. Drying times are significantly reduced and can be more effectively controlled, sanding can be minimized or eliminated, and improved working times and material workability make installation suitable for plasterers of all skill levels—from apprentice to master craftsman.
Continued innovations in acrylic technologies introduced multi-functional materials designed for interior use that function as surface levelers, basecoats, and integrally colored finishes with a wide range of color flexibility and texturing options, from super smooth spray applied to distressed hand applied finishes. Some also serve as joint compounds. Performance options range from standard abrasion resistance to high-impact and abuse resistance—making the design process of creating the most suitable performance and aesthetic combinations within budget easier.
A NEW CATEGORY EMERGES
The evolution of conventional plaster, traditional Venetian, and first generation veneers has now converged to create a new category of Venetian veneer finishing plasters that combine their best features—high performance, aesthetic flexibility, outstanding production rates—which can be increased up to 60 percent, reduce costs and increase profitability.
These water-based, low VOC materials offer many indoor environmental advantages as well. They are breathable and mold and mildew resistant. Their monolithic surface prevents trapping dirt and other contaminants and promotes cleanliness without the use of harsh chemicals or cleaning agents. Meeting the demands of environmentally friendly and sustainable designs, acrylic plasters use minimal energy to manufacture and for both installation and maintenance. They reduce both material use and waste, and help conserve natural resources, using 80 percent less water than traditional plasters during installation. Their ease of cleaning minimizes water usage for in service buildings. By preventing moisture damage, they help protect moisture sensitive building materials and improve the durability and long-term performance of the facility. These acrylic plaster benefits provide for excellent sustainability.
CHOOSE THE RIGHT MATERIALS
With so many options now available, choosing the right combination of materials can be intimidating. The following tips will help ensure intended assembly performance. First, evaluate the appropriate substrate requirements, then build the most suitable Venetian veneer plaster assembly from the base through to the finish. For example, in wet or humid environments, a moisture and mold resistant drywall should be used in conjunction with a waterproof basecoat, the desired performance level of Venetian veneer finishing plaster, and a water-resistant sealer. High traffic or high exposure areas often use standard drywall and an abuse and impact resistant finish to achieve good abuse-resistance, while other more extreme environments require abuse and/or impact resistant wallboard finished with the highest performing abuse and impact resistant finish plaster. By designing a performance plaster assembly from the base to the finish, long-term performance and aesthetics are achieved while reducing expenses associated with maintenance and repair.
Today’s Venetian veneer finishing plasters offer exciting new opportunities in high volume markets—with hospitality, healthcare, education, institutional and multi-family/multi-use presenting the most immediate growth. High volume, spray-applied, multi-purpose, abuse-resistant acrylic plasters over gypsum wallboard, and abuse-resistant veneer finish systems over standard or veneer gypsum wallboard offer the greatest reduction in installation time and costs while improving production rates and project profitability.
Innovation in technology has again breathed new life into the plaster industry and the opportunities are virtually unlimited. Hands on training programs are available and acceptance within the design community is skyrocketing. Take advantage of the opportunities this new category of plasters offers.
Looking for a reprint of this article?
From high-res PDFs to custom plaques, order your copy today!