New Trends in Construction Sealants and Adhesives
Optimizing your use of sealants and adhesives could make you more efficient and profitable.

While coming out of the pandemic was a welcome relief for all, events around the globe and at home have had an immense impact on the day-to-day life of the professional builder and contractor. Costs on materials are stubbornly high, mortgage rates are putting a wet blanket on the housing market, bids for small-scale commercial jobs are crowded, labor consistency and quality remain the top concerns, and many homeowners are spending money on vacations and their lives instead of home repairs. With that said, most contractors will tell you they are keeping busy and always looking to stay profitable in a tough, labor-stricken market.
Amidst these challenges, the importance of adhesives and sealants in construction often goes unnoticed. Yet, understanding their functionality and specifications can substantially improve productivity and profitability on job sites. Here are some recent trends and tips aimed at optimizing efficiency and minimizing callbacks.
Hybrids Gaining Ground as Silicone Supply Gradually Normalizes
While contractors are finally seeing some easing on silicone supply, availability remains tight and prices have been stubbornly high, compared to pre-pandemic norms. This remains true for both acetoxy and neutral-cure silicones used throughout different residential building phases of the job. At least in part due to the disruption in silicone, whether you shop in an aisle, across the counter or online, you are likely to see the terms “hybrids,” “modified polymers” and “paintable silicones” popping up more and more. These hybrid sealants and adhesives continue to find a place in both retail and professional supply outlets due to their silicone-like performance and versatile attributes.
Chemistry professionals would define a hybrid as some variation of a polyether or polyurethane with silane or silicone cross-linking. More simply stated, hybrids or modified polymers can offer exceptional performance properties found in more traditional chemistries, but help bridge well-known performance gaps – such as not being able to paint silicones. Hybrids can come at a premium as well, but if you are focusing on versatility and overall performance, it’s hard to go wrong, as the technology continues to gain traction in both residential and commercial building spaces.
While hybrid technology is more prevalent in the sealants market, it is also becoming much more common in the adhesives market. The adhesive advancements deliver fast bonds, which significantly reduces the amount of clamping and bracing needed on even the toughest and heaviest applications. They can also dispense much easier at colder temperatures than traditional polyurethanes. Most hybrids are 100 percent solid, which means they don’t displace any volume when curing and tend not to create air pockets, which, one could argue, can ultimately affect your bond.
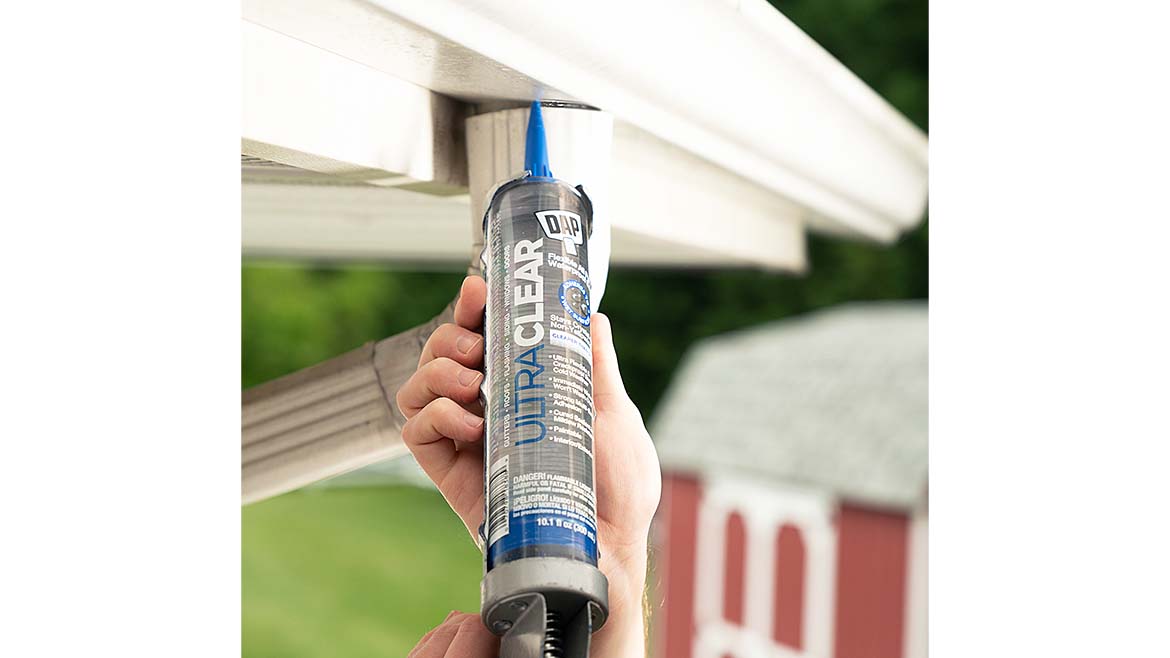
Ultra-Clear, All-Purpose Solvent Sealants are a Dependable Go-To
Contractors and homeowners are increasingly drawn to sealants that offer a blend of ultra-clarity and exceptional versatility, particularly for outdoor applications. Solvent-based sealants have long been a trusted choice, with their advantages and drawbacks well documented over the years. Their unparalleled, crystal-clear clarity makes them ideal for achieving nearly invisible seals, a feat only hybrids can rival.
While not all homeowners may prefer a crystal-clear sealant for every application, they excel in scenarios like through penetrations in foundations, masonry and exterior seam sealing, especially when color matching isn’t feasible. These all-purpose sealants boast the added advantage of being applicable to wet surfaces, making them invaluable for gutter and roof flashing repairs, even in damp conditions. Additionally, they are now available in brush grade, offering quick patch solutions for budget-friendly repairs. Despite their tougher cleanup (requiring mineral spirits), trickier application and stronger odors, these qualities typically pose no issue for professionals. For quick, inconspicuous repairs on exterior surfaces, solvent-based sealants remain unmatched, leading to an increasing reliance on them by contractors.

Wide-Spray Insulating Spray Foams for All?
While large-scale, full-home insulating jobs are still predominantly completed by insulating contractors, we are seeing an uptick in general contractors and remodelers embracing smaller insulating spray foam products for jobs too small either for the insulation contractor or for smaller weatherization jobs. For many years, the complexity of two-part polyurethane spray foam kits has steered them primarily to insulating professionals only, but improved education and marketing materials, as well as a focused push by manufacturers, have now made two-part portable spray foam kits more readily available to general contractors.
Additionally, as inflation remains and budgets tighten, making homes more energy-efficient continues to be a priority for homeowners. These polyurethane systems range in sizes from 12 to over 600 board feet (square feet at 1-inch thickness) and can now be found in more and more retail and lumberyard locations. One advantage of the two-part systems is the reaction speed, which usually creates foam hard to the touch in around a minute. The contractor should be able to create a full air barrier with most brands at around 1-inch thickness and then can place fiberglass insulation right over the top to meet R-value building requirements. This application approach has been coined “flash and batt” and is a cost-efficient way to deliver the benefits of an air and vapor barrier to a batt insulation wall system. In addition, the products now have Low Global Warming Potential blowing agents, greatly lessening atmospheric impact compared to previous systems.
While contractors generally meet this new application opportunity with excitement, it’s important to note a few key things before jumping in. First, it’s vital to read and follow all the instructions provided by the manufacturer. “Reading instructions” isn’t a topic in this trends article because reading instructions has never trended and, usually, professionals can get away with it, but not with these products. This is especially true with temperature. Swings in temperatures of substrate, ambient and chemical on two-part systems can vary your yield significantly and, thus, your bottom line.
We also adhere to the principle that “a little foam goes a long way.” Frequently, contractors tend to spray heavy when all they really need is a thin, consistent layer. Again, check the manufacturer’s guidance on wet applied thickness and the resulting cured state thickness. With some education and practice, contractors can help add these portable insulating systems to their repertoire of tools to help increase profit on their next remodel or extension.
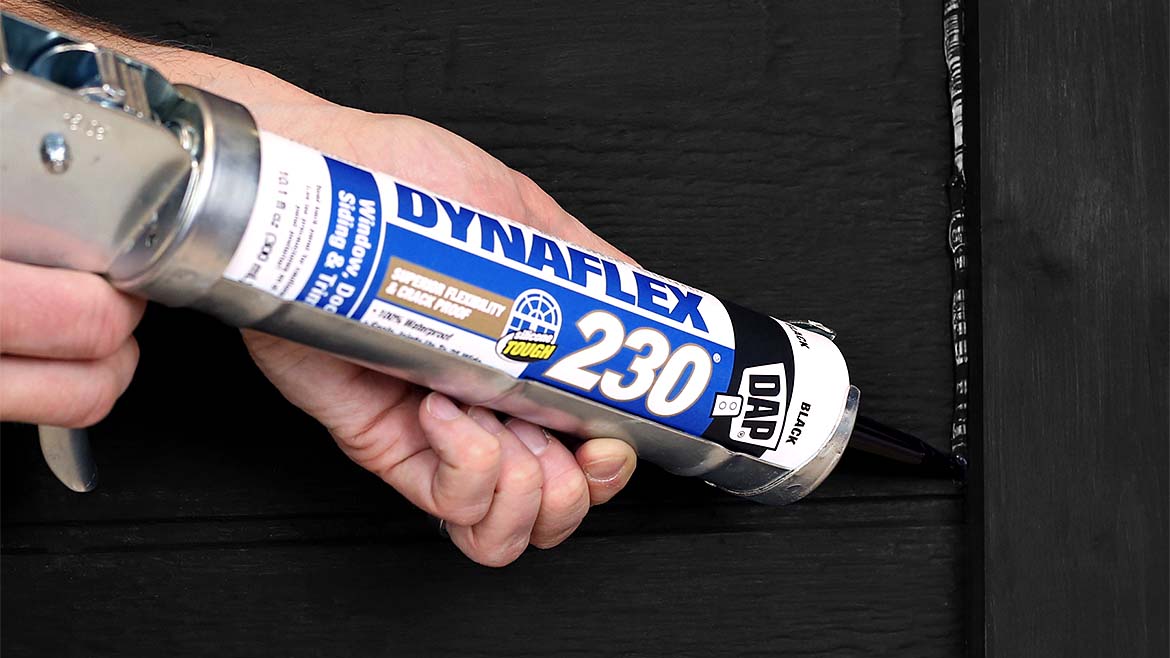
Dark is “In.”
Drive through a new housing development and you are likely to see dark bronze or black windows and doorframes. Mirroring industrial design that has been around for decades, black and dark bronze provide homes with nice contrast against exteriors, blend well with glass, and stand out against traditional windows and doors. As a result, dark finish sealants are also trending, especially black.
While the aesthetics are nice, it’s important to understand the impact that darker building materials may have on your sealants and other building materials. We recommend using a higher-end window, door and siding sealant with specific callouts for UV and fade resistance, as well as exceptional weather resistance. Since darker materials will absorb more heat, depending on the window and door material used, you may experience additional expansion and contraction. As a result, look for window and door sealants with high flexibility on the label or technical data sheet to help adjust to any changes to expansion and contraction.
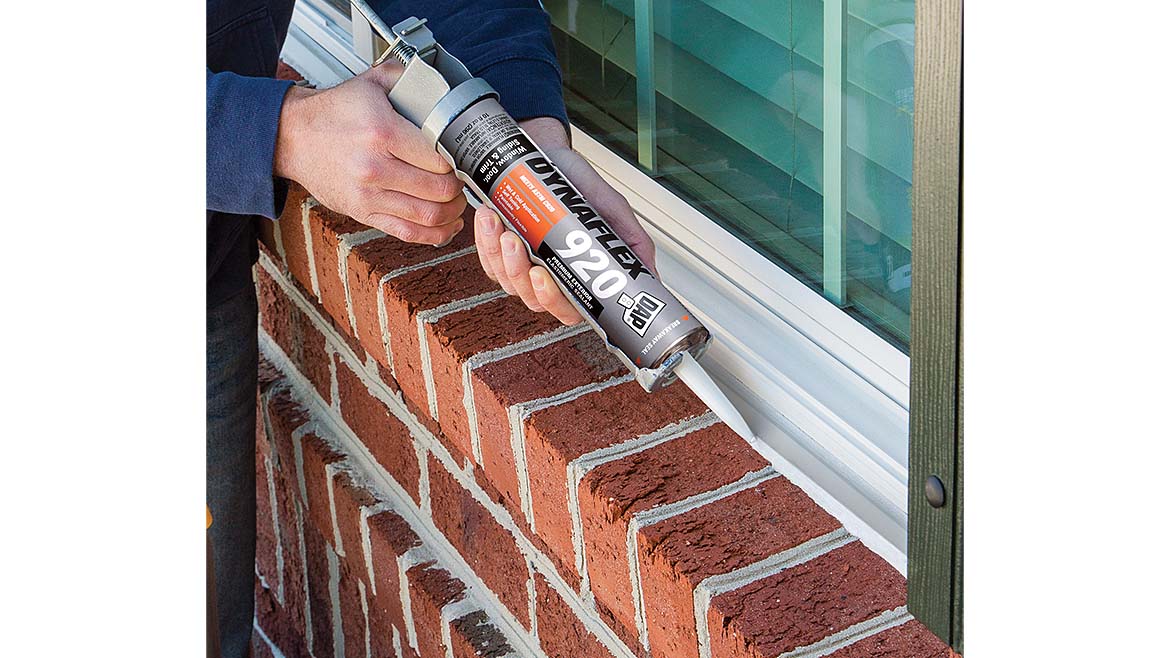
Understanding Flexibility Ratings and ASTM C920 Specification
Sealant manufacturers test flexibility in many ways, but one way to understand the flexibility rating of a product is to look for the ASTM C920 performance specification on either the label or TDS. Sealants that meet C920 face more stringent testing on several different performance characteristics, including flexibility. It’s also important to look at the C920 “class” information, which is a number, usually 12.5, 25 or 35 for residential-construction grade products. When the label says C920 +/- 25, it means the sealant has been tested through multiple cycles of expansion and compression by 25 percent of the original gap size. For flexibility, the higher the class number, the more flexible the product. As higher flexibility usually indicates a higher quality and price, it’s important for pros to understand the right amount of flexibility needed for their jobs. For darker siding and trim, we recommend at least a C920 Class 25 product.
When it comes to the use of adhesives and sealants in the construction industry, product knowledge and selection can go a long way in ensuring a project is completed quickly and correctly for a long-lasting result, eliminating callbacks and boosting your bottom line. Most manufacturers offer a range of tools, tips and technical data sheets on their websites. Don’t hesitate to contact their technical support lines for personalized adhesive and sealant recommendations tailored to your specific jobs. This proactive approach will deepen your understanding of the products you’ve been using for years and provides the opportunity to discover new insights, ultimately saving you time and money.
Looking for a reprint of this article?
From high-res PDFs to custom plaques, order your copy today!