Air leakage in buildings has severe consequences, and we are just beginning to understand their extent. Air leakage in buildings affects almost every aspect of the building’s performance. Air barrier systems positively affect all of the following building envelope issues.
Moisture
Moisture in buildings is at the top of the list for causing moisture problems. It is one of the predominant problems resulting in insurance payouts. Moisture causes premature building failures, increased maintenance costs and too-early replacement.
Moisture can result from liquid moisture getting into the building due to the water not being shed from the building by roofing materials, water-resistive barriers, flashings and waterproofing. Moisture caused by poor construction–materials stored outdoors or moisture from paint and adhesives as they dry—can leave building materials with high moisture content, leading to problems.
We now understand that water damage in buildings may not be from outside liquid water, but from water vapor infiltrating the building assemblies and then condensing. When discovering the damage, the water is in a liquid state, and one may not immediately think that air leakage is the cause. The most common reaction is to believe that the water results from water vapor transmission through the material.
It may be water vapor, but a vapor barrier does not solve the problem, as the air leakage carries the water vapor to the area where the vapor condenses into its liquid state.
People call the roofing company in the late winter, after having no rain for four months and no snow melting on the roof, and demand that the company come to fix the “roof leak.” One roofing company was so fed up with being blamed for shoddy workmanship when they had done a nearly perfect installation of the materials that they refused to install shingles until someone had sealed all the air leaks into the attic.
When the outside temperature is colder than the interior temperature, warm, moist air from the inside can leak through the holes and cracks to the first plane of condensation, where the vapor turns into liquid. When the inside temperature is colder than the exterior temperature, warm, moist air from the outside can leak through the holes and cracks to the first plane of condensation, where the water vapor turns into liquid. It does not matter where you live; you will typically see warm and cold atmospheres yearly in the North or South.
Using an air barrier system in a building reduces moisture problems in hot and humid climates. The amount of moisture transported by air leakage is greater in hot and humid climates than in cold and dry climates.
Moisture in buildings causes mold growth, decay, rot and corrosion that lead to structural problems, durability issues, increased maintenance costs, building devaluation, health problems of the occupants and more.
A complete air barrier system in a building goes a long way in managing moisture problems. Many air barrier materials and accessories can also be water-resistive barriers to provide additional protection.
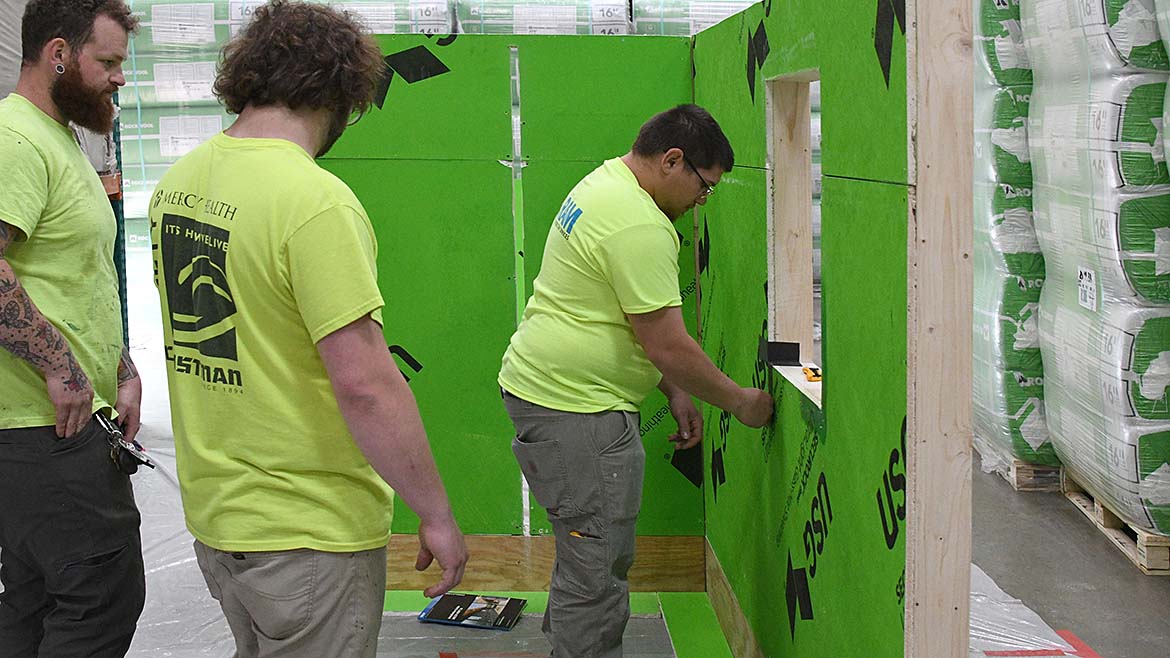
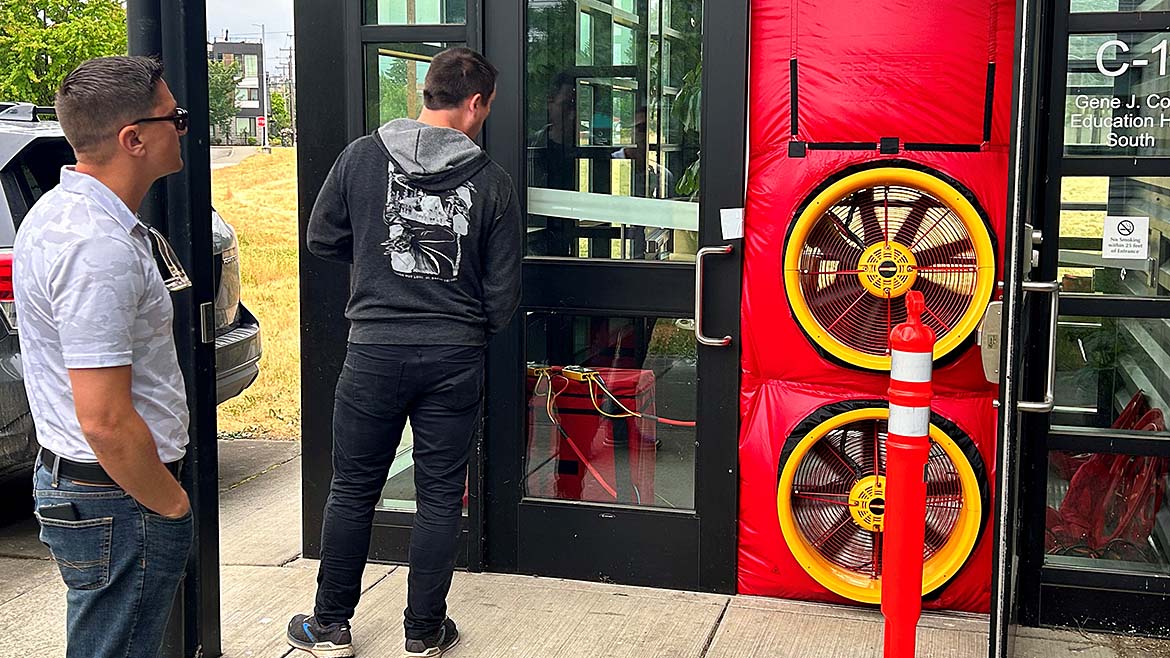

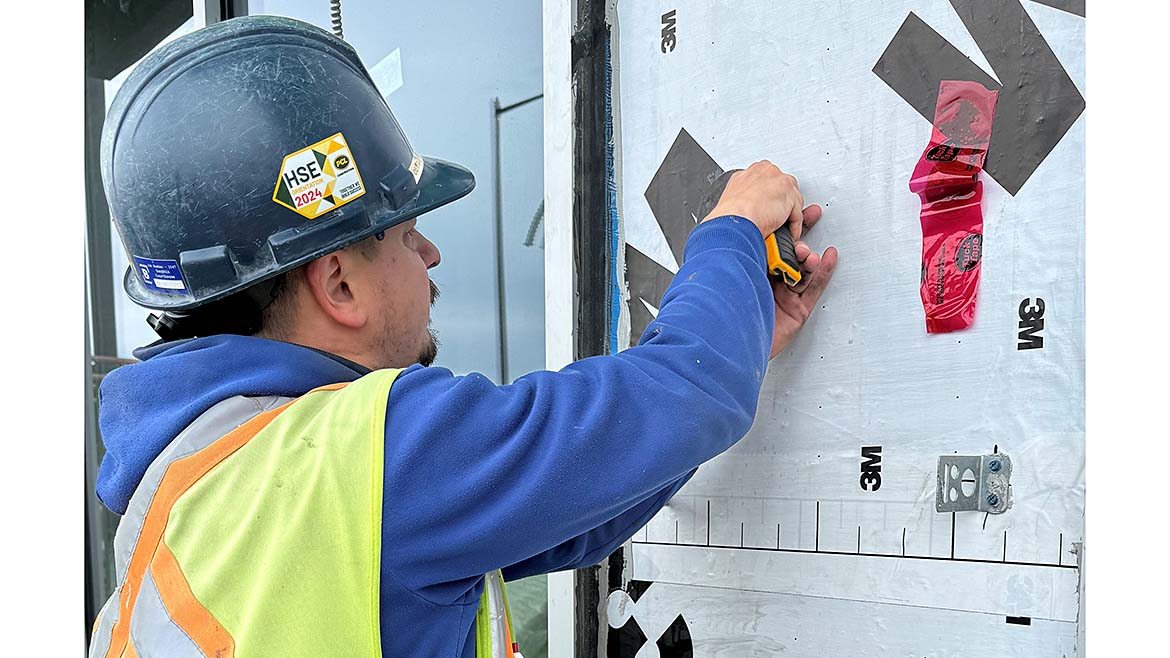


All images courtesy of ABAA
Energy Use
We don’t always want the indoor environment to be the same as the outdoor environment. To make ourselves comfortable, we add or subtract heat or moisture from the air inside the building. When this conditioned air exits the building, outside air replaces the air and needs conditioning. To condition the air, we use energy to add or subtract heat or to add or subtract water from the outside air. The more air leakage in a building, the more air we need to condition and, therefore, the more energy we use.
The National Institute of Standards and Technology reports that the added energy to heat and cool buildings due to infiltration and exfiltration of air can be anywhere from 10 percent in cooling climates to 42 percent in heating climates.
The Building Technologies Office Multi-Year Program Plan from 2010 showed that air infiltration in buildings results in a primary energy consumption of 2.26 quads for heating and 0.59 quads for cooling for residential buildings. Infiltration in commercial buildings results in a primary energy consumption of 1.29 quads for heating and minus 0.15 quads for cooling. Reducing air leakage rates in buildings has a significant impact on reducing energy use. Reducing air leakage in a building provides a double-digit reduction in energy use, whereas almost all other energy-saving measures result in single-digit savings.
Air Leakage’s Impact on Insulation
For fibrous types of insulation, air provides the insulation value. Think of glass. We know that it is not a good insulator, but we spin it into cotton candy and put a lot of it in our buildings. The purpose of the spun glass is to reduce the potential for air moving through the insulation by convection currents. The fibrous insulation minimizes the convection currents in the cavity. However, if air flows through the insulation due to a pressure difference, the fibers cannot stop airflow through a material. The reduction in insulation’s value can be up to 40 percent. Different fibrous insulation types will have different airflow rates; therefore, the drop-in insulation value will differ from material to material. When you combine fibrous insulation with an air barrier, it results in top-performing insulation.
Some designers then switch to an insulating material that does not allow airflow. That can help, but make sure that the air does not flow around it.
Here are two examples. In the first example, a research project was conducted to see the best way to insulate the interior of naval buildings constructed from CMU and turn them into office buildings. On paper, it seemed that the optimal way to insulate was to add polyisocyanurate boardstock insulation over the existing interior gypsum finish and install new interior gypsum boards. That looked good on paper and in computer models. However, what was not considered was that the steel-stud wall in front of the CMU wall allowed air to flow freely behind the steel-framed wall and the CMU wall, rendering all of the insulation ineffective. The problem was solved by compartmentalizing the wall and sealing it between the steel-stud wall, the CMU wall, the ceiling and the floor. The air could not flow between the walls, so the insulation was short-circuited.
The second example happens on many job sites. For example, the project specifications call out rigid, cellular plastic insulation with a higher R-value to be installed on the exterior of a backup wall. During an inspection of the installed insulation, it is observed that the boards do not lie flat against the wall. In many cases, the wall is not level. In other cases, material, such as mortar, was not struck flush or tooled and protruded past the wall’s plane. These imperfections create an air space between the wall and the insulation, allowing air to flow behind the insulation and negating the insulation value of the board. The air can leak from the building or come from the outside, enter the wall cavity and then exit the wall cavity to the outside in a wind-washing effect.
The same physics can happen from the interior. Air can flow into the wall cavity carrying moisture, move through or around the insulation, and either exit the cavity to the outside or return to the building with an indoor air-washing effect.
In all these cases, air moving through or around insulation reduces or negates the value of the insulation, resulting in moisture problems and increased energy use.
Air Leakage Through and Around Fenestrations
Whether the air leaks through a wall or a window, the results are the same–moisture problems and increased energy use. Operating windows and doors can be made very airtight. Some manufacturers are adapting European technology for use in North America. These products are extremely airtight and watertight. Choose extremely airtight and watertight fenestration products for the project.
Nevertheless, purchasing the best fenestration in the world does not mean that it will be installed properly. For many fenestration installers, the job is to ensure that the product is level, square and appropriately secured. Air and water intrusion are not concerns. It needs to be extremely clear in project specifications which trade is responsible for tying the fenestrations to the plane of air and water tightness. This job is left to the air barrier system installer for many projects.
The least insulating part of a window is the window frame. The best insulating value will be found at the center of the glass. In cold climates, if a window is installed in a wall and not sealed to the air barrier assembly, a lot of air leakage can occur from the exterior into the building between the window and the rough opening. In commercial buildings, frames are often steel or aluminum. Cold air flowing past a metal window frame cools the window frame even more, resulting in condensation or frost. The gap between the window frame and the wall air barrier must be sealed.
Air leakage around windows, between the window frame and the wall, is the second-largest leakage area, just after the roof-wall connection.
Sound Abatement
Sound has become a significant concern in buildings. This could be sound from the outside or adjoining rooms, or on the floor above or below. Designers have used air-leakage control techniques for decades to reduce sound travel. Most of the sound we hear travels through the air. If we stop the air from traveling, we stop much of the sound. Air barrier systems are seeing increased usage on both the exterior and interior, between dwelling units or offices, to prevent air movement and, therefore, sound.
Odor Abatement
Most people don’t want to know what their neighbor cooks every night. In multi-use commercial buildings, there are times when odors from one unit seeping into another unit are undesirable. One real-life example was in a strip mall. One of the tenants was operating a beauty parlor that used many chemicals, and the unit next door was a pet store. The fumes from the beauty parlor seeped over to the pet store and bothered the animals to the point that they made a lot of noise.
An interior air barrier between the two units resulted in the odors being contained within the unit.
In today’s world, more and more people are becoming sensitive to odors and demanding that their living environment be separated from others.
Pollutants
Pollutants are a broad description that covers so many items. Many consider water to be a pollutant, for example. But, for this discussion, the focus is on airborne pollutants.
The air, both inside and outside the building, carries airborne pollutants. They include pollen, suspended particulates, allergens, bacteria and smoke. Exterior airborne pollutants can be brought into a building and become concentrated inside.
In addition, pollutants or materials in a building can become airborne. They can include mold spores, bacteria, asbestos fibers and rodent droppings if air moves through the building envelope, crawl spaces, attics, storage areas and garages. It can pick up many of these materials and bring them into the living space, where humans or animals can breathe them.
Another pollutant is dust. Depending on the day, there can be a lot of dust in the air, even if it is not visible. As outside air leaks into a building, it brings dust with it. This dust circulates throughout the building, eventually settling on the furniture, walls, floor and anything else inside. Occupants of airtight buildings notice the lack of dust inside the building.
HVAC Efficiency
Upon entering a building, the first thing to realize is that the HCAV will not work without a building envelope. Then, we need to understand that we must build the building envelope tight and ventilate it right. Air that is necessary for the occupants of the building needs to enter through the mechanical system and not through holes and cracks in the building envelope.
The building envelope needs to be completely airtight if we want the HVAC system to work as intended. If we have considerable air leakage in different parts of the building, delivering the right amount of air to the right rooms will be impossible.
Pressure balancing of the distribution system and checking airflow from each register will not solve the problem. The pressure difference between the inside and the outside of the building will vary from hour to hour, so the procedure may have to be repeated an hour after it is adjusted and the whole system re-balanced.
For an HVAC system to work correctly, the building envelope must be completely airtight and each space must be separated from the others. This means compartmentalizing buildings, room from room and floor from floor. Air-sealing each floor turns a 12-story building into 12 one-story buildings, as far as stack pressure is concerned.
Changes in air pressures in a room can disrupt the delicate pressure relationships between conditioned spaces that HVAC systems create by design. This could happen in buildings like hospitals, where infection control and patients’ very lives may depend upon maintaining those relationships, and laboratories, where pollutant control is essential.
Insects
Insects like the interior conditioned space as much as we do. They are drawn to air leakage spots and enter the building through the holes and gaps. Air leakage around windows is one area where they enter, resulting in a school building being infested with flies. The building was air-sealed to stop the flies from entering, but work was justified as making the building more energy-efficient.
Much has been learned about air barriers and their value in creating creature comfort and saving energy.