Industry Voices
Outside Out or Inside In?
Water-resistant barriers vs. air barriers in modern construction.

The more I teach and peer-review plans, the more I realize how confused the architectural and engineering communities are when it comes to the roles of air and moisture/water barriers in modern construction.
My elevator pitch for weather barriers—and really the entire exterior building envelope—is that it is the system—a combination of products, materials and subsystems—keeping the outside out. The codes refer to the weather barrier as a water-resistive barrier, so for the sake of consistency, we will adopt that term. Our view of an air barrier is just as simple; it is the system keeping the indoor—conditioned air—in.
Residential and Commercial Applications
In residential applications, the WRB is typically located behind the cladding of drainable wall assemblies. There is not a WRB, per say, in the floor or roof assemblies, though the under-slab vapor barrier and roof underlayment serve similar roles. The key takeaway here is that the vapor retarder, WRB and roof underlayment are not a contiguous system in this application. The air barrier is typically located on the interior side of the structural shell. Components of the air barrier would include the floor deck, interior wallboard, windows/doors and interior ceiling panels. Although this system is contiguous, it has hundreds of planned penetrations through it from MEP devices.
In commercial applications, the WRB is typically located behind the cladding of drainable wall assemblies. Although a WRB is not identified in the floor or roof assemblies, current industry standards would have it sealing to the floor and roof systems, such that it is contiguous. As such, in commercial buildings, the WRB and the air barrier can and should be the same. Components of the combined WRB/air barrier would include the foundation, damp-proofed sheathing with an air barrier product, windows/doors and roof system. Although this system has penetrations, they are not near the amount of the residential example and can be sealed in a more aggressive fashion since they do not affect aesthetics (i.e., they are not on the face of an interior wall).
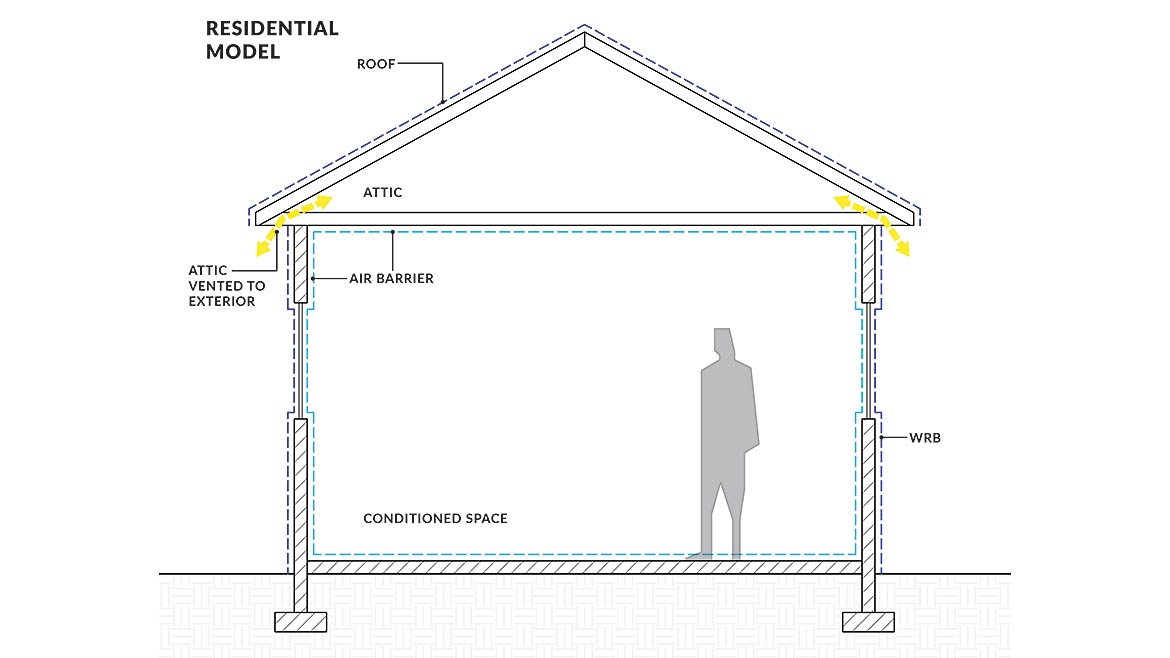
Which Model Should I Use?
All that said, there are residential buildings that follow the commercial model offered and there are commercial structures that follow the residential model. The important part is to be able to identify the air barrier and detail accordingly. A poorly designed and detailed air barrier can allow for condensation, potentially allowing the premature degradation of building materials and indoor air quality.
With that in mind, is one model better than the other? Does it differ from cold climates to hot climates? Well, depending on where you are, the answers may change, but here is my position and why.
The Pressure Is On
Positive pressurization in a mechanically climate-controlled building is paramount. If a building is positively pressurized, the building envelope can survive minor imperfections in workmanship related to the exterior building envelope, as moisture on the drainage plane from rain or condensation is simply pushed away. The air barrier is how the building maintains pressure to provide that protection. Alternatively, if a building is allowed to operate under negative pressure, moisture can migrate into spaces where materials are not water-resistant, fostering both structural and air quality concerns. So, as an architect, I want as much of my structure inside that air barrier as possible, no matter where I am designing geographically. As a side bar, I also want the air barrier to be robust and easy to repair without aesthetic concerns.
There is no doubt that two decades of providing litigious support on cases related to the exterior building envelope has influenced my peer-review comments and the way I design buildings. I have seen hundreds, if not thousands, of buildings where the structure and/or the IAQ has deteriorated via a poorly designed exterior envelope. Air barrier placement is a design issue. Workmanship and the best “can of air barrier” (long story—another day) will not correct bad design.
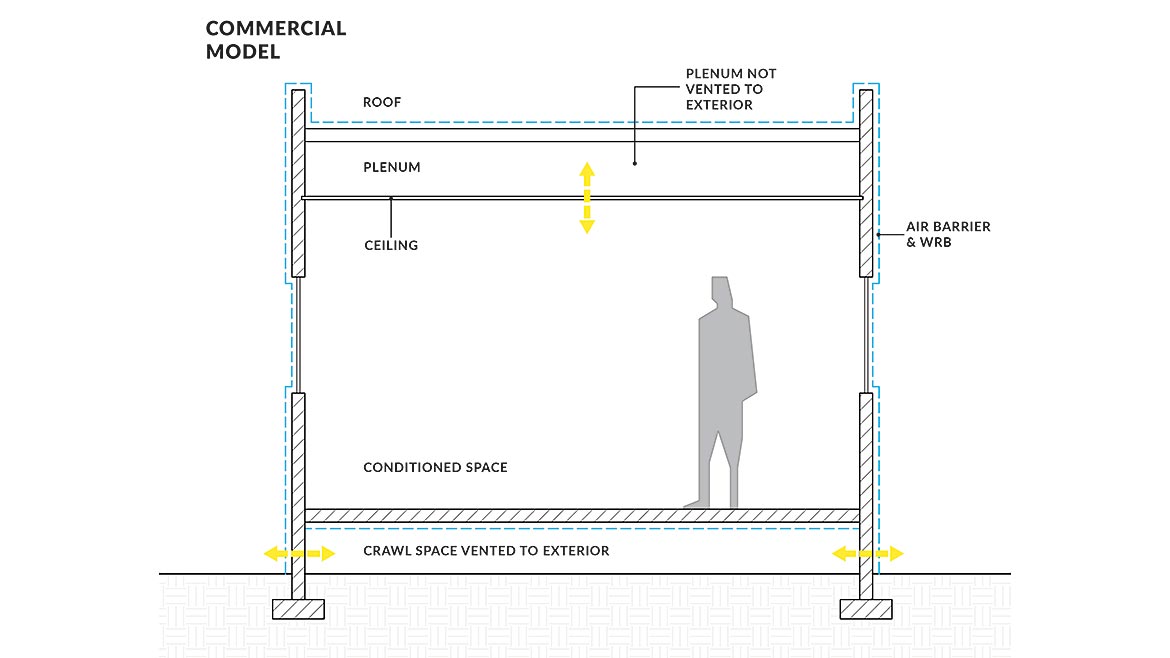
Why is Positive Pressurization Important?
As far as a case study, here is one I can share. We were evaluating a large building a few years back that was experiencing some significant water infiltration issues. Our usual protocol is to sample some percentage of windows for water infiltration, per ASTM E1105, and perform blower door testing to see if the building is “leaky” from an air standpoint. Well, the windows leaked right on cue, but the blower door passed with excellence. It was a new building, and the design intent was for it to follow my commercial model.
What we discovered was that windows had been sealed to the cladding, not the WRB, so the seal from the interior wallboard to the window system was now part of the air barrier. The materials were new, so even though they were not moisture-resistant, they had not deteriorated from exposure. When we cut the interior seal, water ran out and, upon further review, we could see organic growth along the backside of the interior wallboard. We also held a “tell tail” (i.e. tissue) up to the joint and noticed that the building was under negative pressure when the HVAC was re-energized.
I think of this condition every time I look at a traditional house. The WRB is not contiguous—the soffit and other passive vents ensure to that—the predominant air barrier is a material (gypsum wallboard) that is not moisture-resistant and supports organic growth, and the building is operating under negative pressure. Oh, and the framing is a wood product that is also not moisture-resistant. Just awesome. No wonder mold is gold.
Looking for a reprint of this article?
From high-res PDFs to custom plaques, order your copy today!